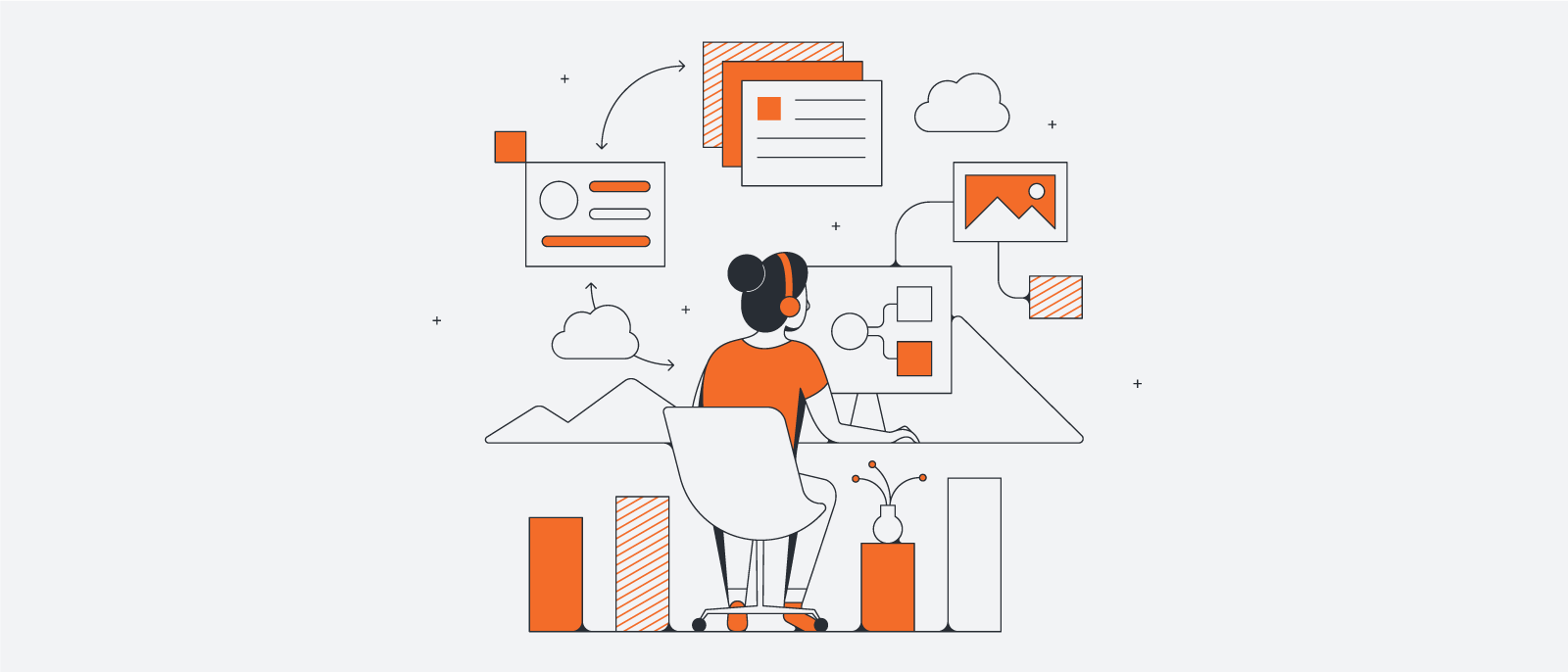
Quality assurance vs. quality control: What are the differences?
Lucid Content
Reading time: about 8 min
If you’re confused about the difference between quality assurance (QA) and quality control (QC), you’re not alone. Many professionals believe the two terms are interchangeable. It’s true that QA and QC are related and each is a very important part of product development. But the two roles differ in their approaches to ensuring that your company consistently delivers quality products.
Let’s examine the difference between quality control and quality assurance so that you can confidently implement a system that uses both roles to meet customer expectations, needs, and requirements.
What is quality assurance (QA)?
Quality assurance is part of the ISO 9000 set of international quality management standards that help companies meet compliance requirements, satisfy customers, and continuously improve processes and procedures.
The QA role looks at the processes and procedures during a product’s development or manufacturing to identify and address possible problems before they happen. The idea is to find ways to improve processes and procedures in an effort to prevent defects, bugs, and other problems from being introduced into your products. The more you prevent errors, the happier your customers will be.
QA can be applied to everything from manufacturing to construction to software development and to organizations of any size.
What do quality assurance professionals do?
People working in QA are responsible for planning and implementing the processes, procedures, and best practices that your employees need to follow when developing your products. The QA team also defines how and when to monitor and audit processes to ensure that development runs smoothly, problems are fixed quickly, and that improvements and adjustments are made as needed.
As a QA professional, you may be asked to:
- Plan, develop, and implement quality assurance policies, processes, and procedures.
- Document and update SOPs and best practices.
- Audit processes and procedures to make sure that regulations and standards are met.
- Monitor current processes to look for ways to make improvements.
- Train production and engineering teams to ensure that established processes and procedures are followed.
- Perform root cause analysis and implement solutions that address problems found in current processes and procedures.
- Inspect raw materials used in manufacturing.
- Collect and evaluate feedback from customers.
- Ensure that your documented processes comply with industry standards and regulations.
Why is QA important?
By focusing on development or manufacturing processes, QA helps your company to establish customer confidence. Customers are more likely to continue buying from you if they perceive that your products and services meet high-quality standards, adhere to regulations, meet their expectations, and address their specific needs.
Ultimately, you want your quality assurance processes to give you reliable and repeatable results so you can produce quality products and services that your customers want and can trust.
Quality assurance example
When you go to the doctor, you might get annoyed that several different doctors and nurses keep asking for your full name, date of birth, address, and the procedure you will have done that day. Can’t they just check the wristband they gave you when you checked in?
They ask these questions multiple times as a quality assurance procedure to ensure that they are providing the correct treatment for the correct patient. It’s better to be annoyed by a few questions than to wake up and find that they “fixed” your knee when they were supposed to work on your shoulder.
What is quality control (QC)?
Quality control is also part of the ISO 9000 set of quality standards. The QC role looks for defects and bugs after the product is built.
QC is used in software development to identify bugs or features that don’t work as planned. In other industries such as manufacturing and construction, QC is used to inspect products to make sure there are no blemishes, weak spots, defects, missing parts, etc.
What do quality control professionals do?
A QC professional inspects or tests products to ensure that they function as expected, that there are no defects that could cause injury, and that the products are ready to be released to the market.
A QC professional may be asked to:
- Evaluate and recommend testing software.
- Set up automated testing to make sure that the products measure up to established requirements and expectations.
- Look for defects, blemishes, or errors that could damage customer trust in your products.
- Make sure that the final product is in compliance with company standards and federal and state regulations.
- Write and maintain testing and inspection reports, noting any deviations from established standards and expectations.
- Identify and document bugs and defects that need to be fixed before a product can be released.
- Identify and document bugs and defects that can be fixed after the product has shipped.
- Test documented assembly and installation instructions to ensure that customers can safely assemble products as described.
- Work with QA professionals to help identify areas that could use improvement.
- Evaluate customer feedback and complaints, focusing on finding and recommending solutions that will make them happy.
- Ensure that only high-quality products are released to market.
Why is QC important?
There are a lot of companies making products that are similar to yours. It is important that you establish good QC practices because consistently releasing high-quality products is a good way to differentiate your products from others.
Releasing products that are easy to use, work as advertised, meet expectations, and require little or no post-sale support, builds trust and brand loyalty. When you have a happy, loyal customer base, they will likely purchase new products from you based on positive past experiences. And they might encourage friends and family to give your products a try as well.
Quality control example
Your company makes overhead garage storage racks. Each rack can hold up to 400 pounds. In an effort to cut costs, you are testing new material in the bottom of the rack to hold the storage items. The vendor who supplies the material insists that it can hold up to 400 pounds. Your testing of the new material confirms that it will hold 400 pounds. But after a few months, you get customer complaints that the material at the bottom of the rack is bulging under the weight of the storage items. This compromises the safety of your product.
You implement a new plan that will last for a few months to test the integrity of the material at the bottom of the rack. The results show that after three months, the material weakens and starts to bulge. The material could eventually break and lead to property damage and injury. In your report, you recommend returning to the original material while looking for a stronger, cheaper alternative.
QA vs. QC
We’ve discussed that QA and QC are not the same thing and should not be used interchangeably. But the two roles are dependent on each other. You can’t have QC without QA. Sure, you can do QC testing of your products after they are developed and report the defects and bugs you find, but that doesn’t do anything to help you refine the processes that created the defects.
Proactive vs. reactive
Quality assurance is proactive. QA professionals proactively monitor and audit existing processes and procedures in an effort to eliminate errors and issues that could become major problems.
Quality control is reactive. QC professionals do their work after the product is built and before it has shipped. They look for defects in manufactured products and bugs in software products. Then they report their findings so the problems can be fixed.
If QA is effective, the result should always be a high-quality product. If QC finds issues, that should trigger a QA review to look at where processes can be improved.
Process vs. product
Because QA focuses on preventing problems before they happen, it is process-oriented. Because QC focuses on finding defects in the product after the processes have completed, it is product-oriented.
QA processes include:
- Documentation
- Audits
- Training
- Active process monitoring
QC procedures include:
- Inspection
- Product sampling
- Lab testing
Creation vs. verification
Part of the role of QA is to plan and design a sort of roadmap that includes everything that employees need to know and do to create high-quality products. This includes defining and documenting the policies, processes, and procedures that all employees need to follow to create high-quality products. It also should include things like product design standards, packaging, manufacturing, coding, assembly, distribution, sales—anything that should be included in the creation of the product.
The QC role is to verify the quality of all of these various items to ensure that you can safely and confidently distribute the product to your customers.
Full team vs. dedicated personnel
The planning, designing, and process monitoring that QA performs is a team effort. The whole team is responsible for maintaining and updating SOPs, making sure that employees are trained, giving employees the resources they need, and following the processes and SOPs to produce high-quality products.
While there may be a team of QC professionals, they generally work alone when testing products. Each QC team member follows SOPs to test the specific products they have been assigned or to test specific parts of a product. They document what they find based on the SOPs for product testing and validation.
Quality assurance and quality control are important and required parts of an effective quality management system. QA and QC can help you:
- Consistently release high-quality products.
- Continuously improve processes and procedures to ensure high-quality standards are met.
- Gain customer trust and loyalty, which will encourage them to buy more of your products in the future.
- Optimize the use of existing resources and reduce costs.
- Proactively find and address issues before they become major problems.
- Increase proficiency and shorter time to market.
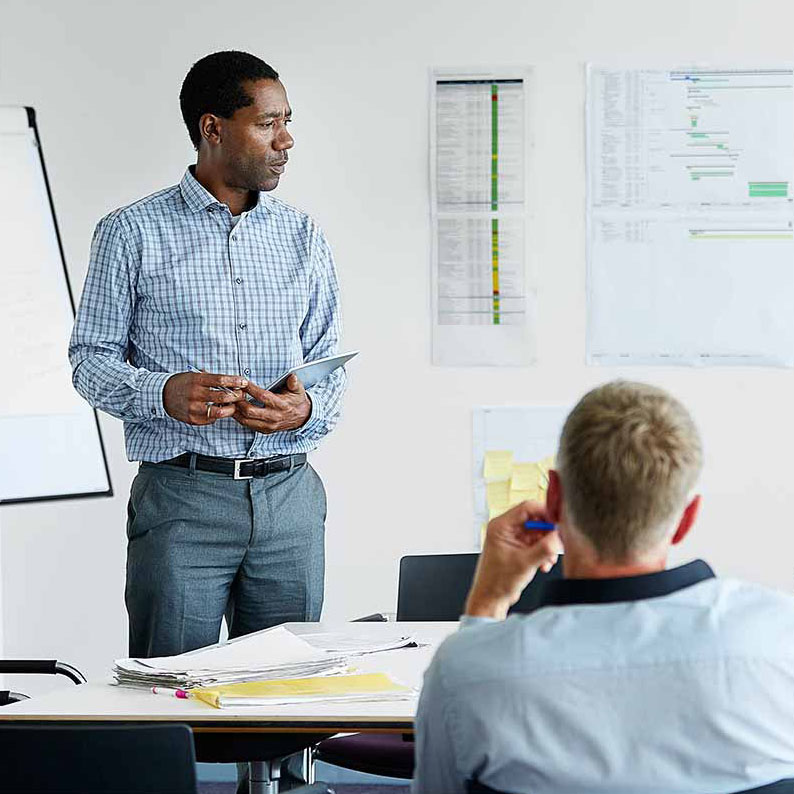
There are 7 essential quality management tools you need to know. Are you using them at your company?
Find outAbout Lucidchart
Lucidchart, a cloud-based intelligent diagramming application, is a core component of Lucid Software's Visual Collaboration Suite. This intuitive, cloud-based solution empowers teams to collaborate in real-time to build flowcharts, mockups, UML diagrams, customer journey maps, and more. Lucidchart propels teams forward to build the future faster. Lucid is proud to serve top businesses around the world, including customers such as Google, GE, and NBC Universal, and 99% of the Fortune 500. Lucid partners with industry leaders, including Google, Atlassian, and Microsoft. Since its founding, Lucid has received numerous awards for its products, business, and workplace culture. For more information, visit lucidchart.com.