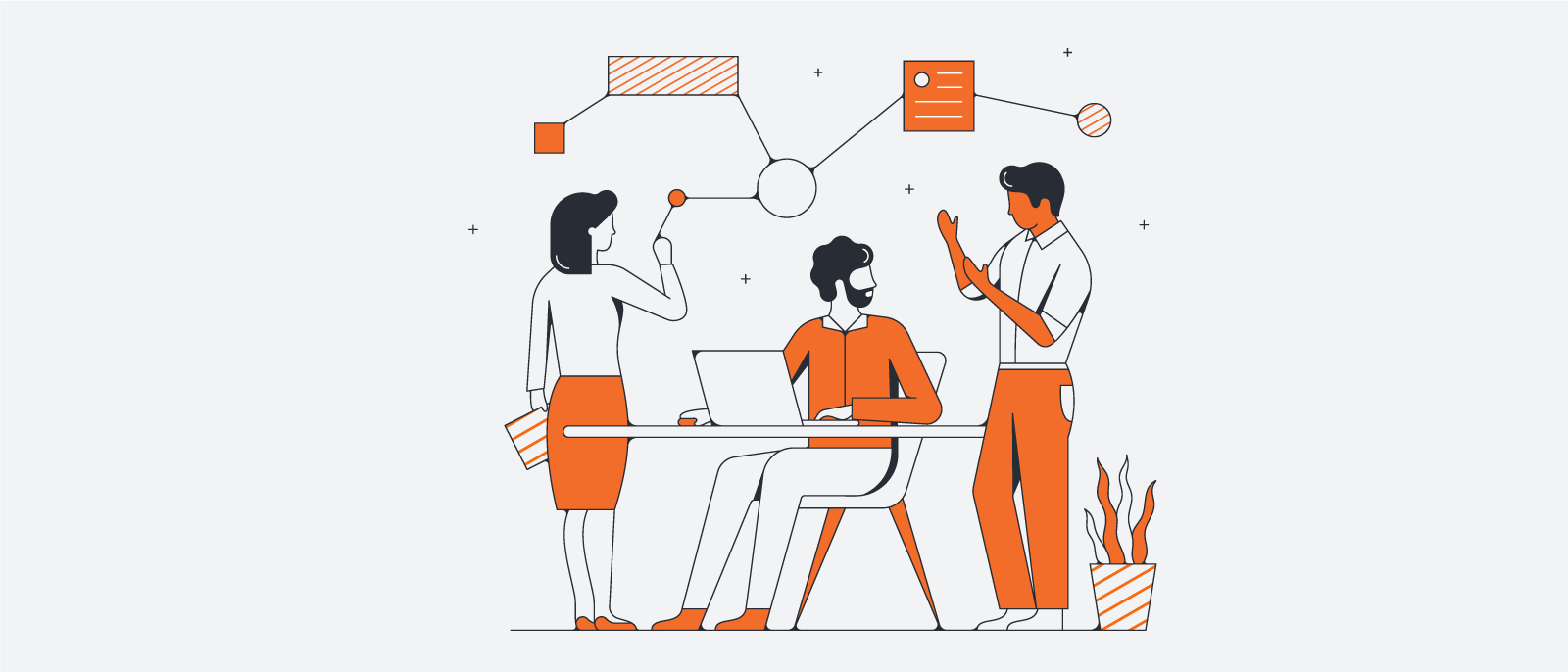
What is Total Productive Maintenance (TPM)?
Lucid Content
Reading time: about 8 min
Topics:
In a perfect world, machines would never break down, assembly lines would never stop, superior products without defects would be produced, product quotas would always be met, and products would be picked up and delivered on time.
But, unfortunately, it’s not a perfect world. Sometimes things happen that throw production off schedule.
This is where Total Productive Maintenance (TPM) comes in. TPM refers to the idea that operators are responsible for cleaning, maintaining, and improving their workstations to ensure safety and quality during production cycles. With TPM, the goal is to keep equipment working in optimal condition so that production processes move smoothly without breakdowns or delays.
What is TPM in Lean manufacturing?
Like many methodologies used around the world to improve workflow, increase production, increase quality, and decrease time to market, TPM was developed in Japan. It’s a natural extension of Lean manufacturing because TPM is also aimed at eliminating waste.
Total Productive Maintenance engages all employees in the effort to eliminate waste by improving the operation, reliability, and efficiency of equipment used to manufacture products. TPM shifts the responsibility of routine and preventative maintenance from members of the facilities or maintenance team to the operators who actually work with the equipment. This puts the people most familiar with the equipment in charge of making sure it runs at peak performance.
When implemented properly, TPM tries to achieve the following goals:
- No equipment failures
- No stops
- Faster and smoother production
- No defects
- Lower operating costs
- A safer working environment
It’s similar to performing routine maintenance on a car. Regularly changing the oil, checking the belts, changing the air filter, and rotating the tires is cheaper than paying full price to fix a neglected car.
The eight pillars of TPM and 5S foundation
The TPM model is built on a 5S foundation—a set of five activities that are used to improve workplace organization, reduce waste, and increase operating efficiency. Each principle begins with the letter S.
On this 5S foundation, TPM erects eight pillars that encourage proactive and preventative measures that improve equipment performance and reliability.
5S methodology
In the early 1900s, Henry T. Ford introduced the principle of CANDO, an acronym that stands for Cleaning up, Arranging, Neatness, Discipline, and Ongoing improvement. About 50 years later, representatives from Toyota visited Ford to learn how to mass-produce automobiles.
The Toyota team was impressed by the CANDO principle and adapted it for their purposes as 5S: Seiri, Seiton, Seiso, Seiketsu, and Shitsuk. These have been loosely translated into English as Sort, Set in order, Shine, Standardize, and Sustain—the 5 Ss.
Sort
This activity involves removing the things that are not needed in the workspace. For example, it’s important to eliminate outdated materials or broken equipment that might otherwise get in your way. In addition, operators should sort equipment and materials by frequency of use.
Set in order
In this activity, operators put everything in its proper place. This makes it easy to find each item quickly and reduces time wasted.
Shine
Operators clean their workspace, equipment, and tools regularly to remove dust and dirt. Buildup of dust and dirt can cause deterioration and corrosion which can cause machines and other equipment to break down over time. Cleaning also promotes safety because it can help to prevent accidents.
Standardize
This activity involves setting standard procedures for performing the first three 5S activities. All employees need to be aware of the standards and should strictly adhere to them. Checklists and audits help to ensure that operators complete tasks as they have been documented in a standard operating procedures guide.
Sustain
When things are running smoothly, teams should still meet regularly to review and audit current operations and find where improvements can be made.
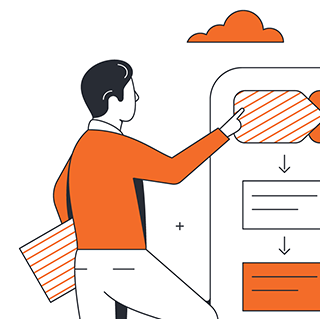
Learn more about 5S methodology, including how to implement it and which tools to use.
Read nowTPM pillars
There are eight pillars of TPM that are built on the 5S foundation. These pillars rely on operators, the people who work with the machines and equipment every day, to perform proactive and preventative measures to improve equipment reliability.
Autonomous maintenance
Each operator has the responsibility for cleaning, lubricating, inspecting, and maintaining the machines and equipment they work with every day. This encourages employees to take ownership of the equipment they use, helps them learn more about how the equipment operates, and frees up maintenance personnel to work on more pressing matters.
Planned maintenance
Planned or preventive maintenance is performed on schedules that are based on predicted or previously measured equipment failure rates. Planned maintenance also takes into consideration the age of the machine and how much it is used. This type of maintenance is done to prevent machine failure and unplanned downtime.
Quality maintenance
This involves monitoring machine performance to detect and prevent equipment errors during operation. Use automated programs to do this to free up employees to work on other tasks. When errors happen, do a root cause analysis to identify and eliminate the problem.
Focused improvement
Small teams of stakeholders are formed to analyze production activities so they can identify and remove anything that does not add value to the process or the final product. This method is meant to continually improve equipment operation.
Early equipment management
Design improvements are made to equipment based on experience and knowledge gathered from previous production and maintenance activities. Work with team members, suppliers, equipment manufacturers, and other stakeholders to ensure that new machinery is able to meet planned performance levels.
Training and education
All employees from senior management to operators need to be trained in TPM methodologies so there are no knowledge gaps that could keep the organization from reaching its goals.
Safety, health, and environment
A safe and healthy work environment for all employees is a critical facet of TPM. Safe and healthy workers have better attitudes and are more productive. Providing a safe work environment helps to keep the workplace accident-free.
TPM in administration
TPM principles should extend beyond the production floor. Office workers, administrators, and managers can apply TPM techniques in the office to increase productivity and reduce waste. For example, TPM can help people determine whether all the meetings on the schedule are really necessary.
What are the benefits of TPM?
Going through every workday with no breakdowns, no defects, and no accidents is the dream. The benefits of the TPM model can bring organizations closer to that dream.
1. Fewer work stoppages due to unplanned maintenance time
When employees take ownership of equipment maintenance and keep workstations orderly, productivity increases. The line does not have to stop as often to identify and fix errors because preventive maintenance reduces errors and defects and ultimately increases uptime.
2. Safer work environment
Adhering to TPM methodologies ensures clean, ordered, sorted, and standardized workspaces that promote a safe and healthy work environment. TPM reduces clutter and movement to minimize accidents. Fewer accidents and a safer workplace lead to higher productivity.
3. Increased output and product quality
Longer uptimes due to safe and well-maintained work environments result in higher quality products and increased customer satisfaction.
4. Reduced costs
When employees buy into 5S and the pillars of TPM, shorter downtimes, safer work environments, and increased output and product quality all result in lower costs.
TPM implementation
Implementing TPM does not happen overnight. A lot of planning and some patience is required to get things up and running. It takes time to train employees to maintain their equipment and organize their work areas, especially if the concepts are new to them.
The following are five steps to implement TPM methodologies.
Step 1: Identify a pilot area
Don’t try to change over the whole plant to TPM all at once. Instead, pick a small pilot area that will benefit from TPM activities. For example, you might begin in an area with older machines or that experiences frequent breakdowns. Get an idea of what can be done to the current equipment and evaluate whether new pilot equipment can be used.
Step 2: Restore equipment to prime operating condition
Train the people who will be using the equipment to focus on an autonomous maintenance program to restore existing equipment to optimal working condition. Use the 5S methodology to clean and maintain the work area. Consider using the 5S dashboard below to track which tasks have been completed.
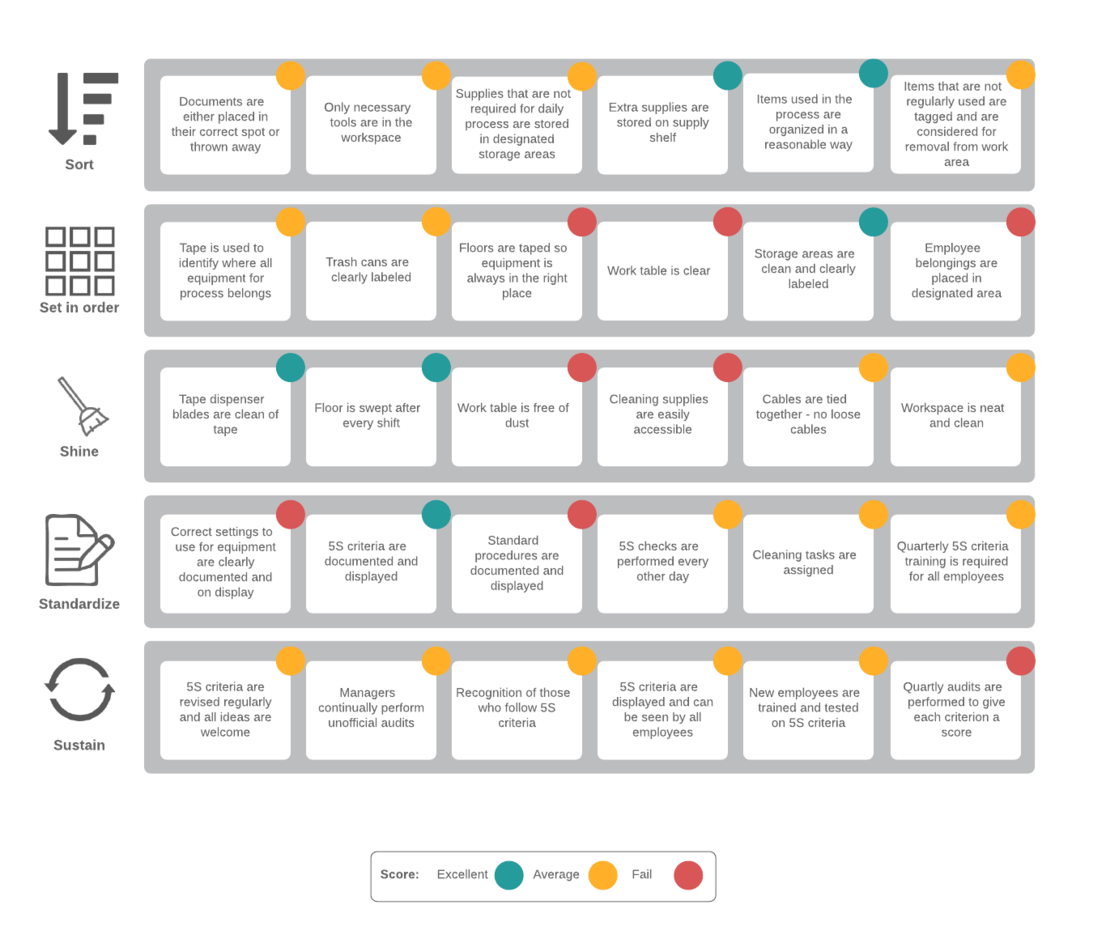
Step 3: Measure overall equipment efficiency
TPM includes exploring ways to increase overall equipment efficiency (OEE). OEE is a measure of how well equipment is working compared to its full potential, its availability, and its scheduled operating time. OOE metrics are used to track progress towards the goal of perfect production.
Step 4: Address and reduce major losses
Overall equipment efficiency uses the Six Big Losses categories to measure common causes of lost productivity.
- Unplanned stops
- Setup and adjustments
- Small stops
- Slow running
- Production defects
- Reduced yield
The TPM pillar labeled “Focused Improvement” can be used to analyze and uncover why these losses happen and locate the best solutions.
Step 5: Apply proactive maintenance
One of the most important principles of Total Productive Maintenance is proactive maintenance—regular, planned maintenance that is performed by the people who operate the machinery. This gives employees a better understanding of what is needed to keep the machine running at peak performance, and it gives them a better understanding of how the machine operates.
Applying TPM principles can dramatically impact your productivity, workplace safety, and processes. When combined with other frameworks and practices, like Lean manufacturing and the 5S methodology, TPM has the potential to improve your workplace environment and your bottom line.
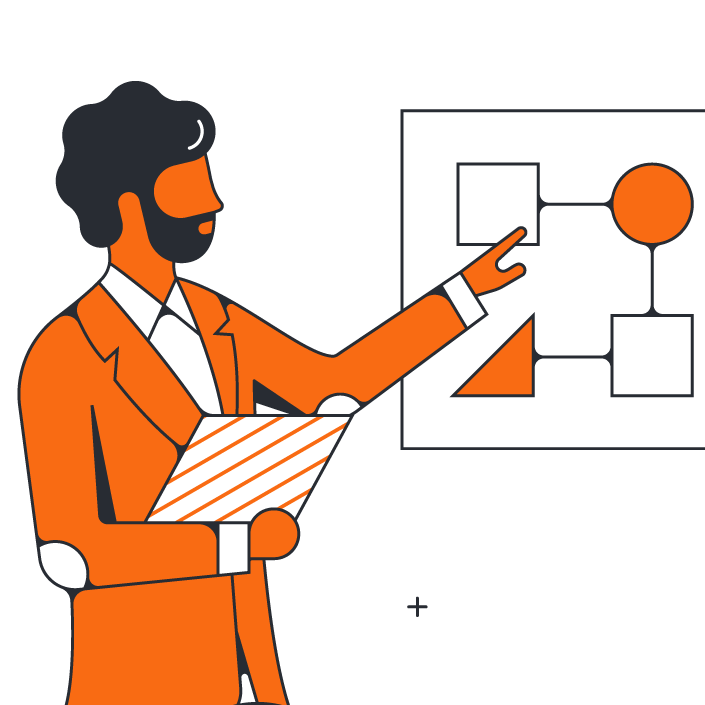
See which tools you can use to accomplish these steps and implement TPM.
Read moreAbout Lucidchart
Lucidchart, a cloud-based intelligent diagramming application, is a core component of Lucid Software's Visual Collaboration Suite. This intuitive, cloud-based solution empowers teams to collaborate in real-time to build flowcharts, mockups, UML diagrams, customer journey maps, and more. Lucidchart propels teams forward to build the future faster. Lucid is proud to serve top businesses around the world, including customers such as Google, GE, and NBC Universal, and 99% of the Fortune 500. Lucid partners with industry leaders, including Google, Atlassian, and Microsoft. Since its founding, Lucid has received numerous awards for its products, business, and workplace culture. For more information, visit lucidchart.com.