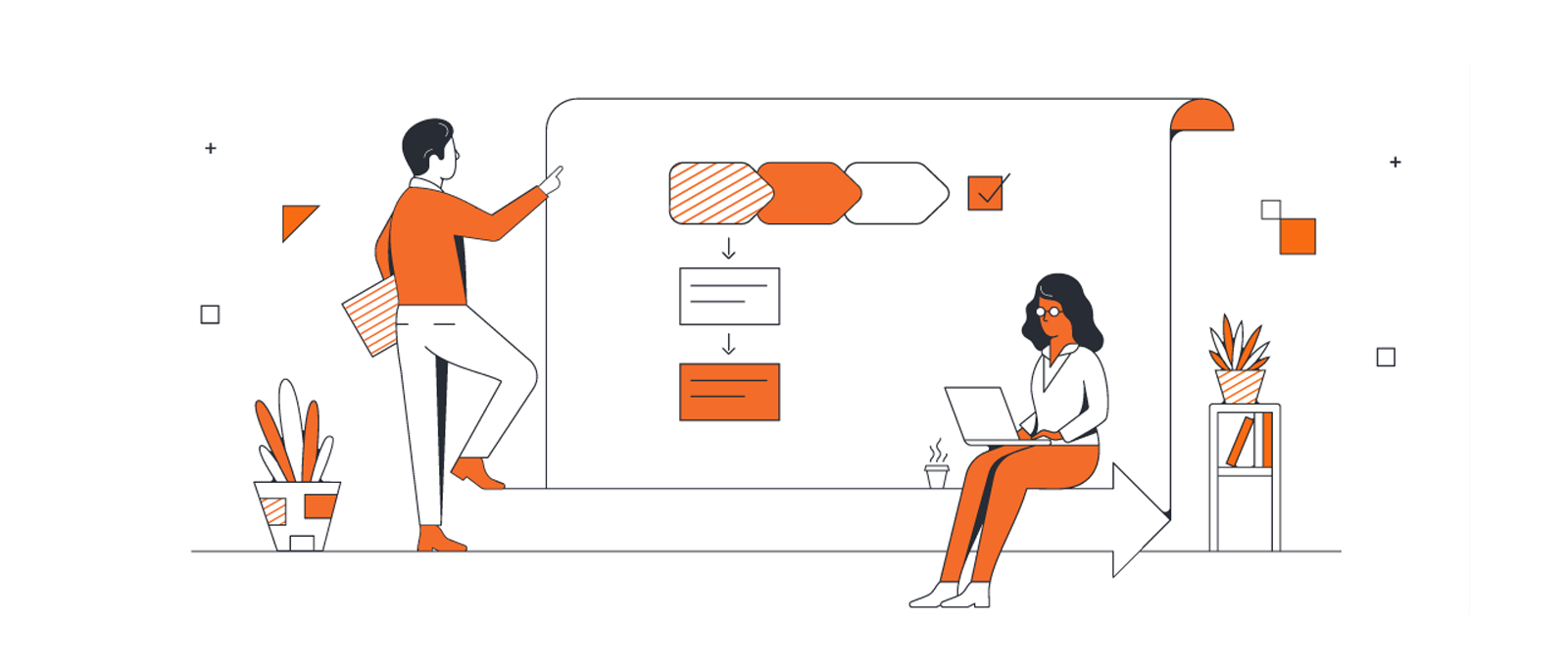
Setting up standardized work and Lean manufacturing
Lucid Content
Reading time: about 9 min
Topics:
In an episode of the TV show “Superstore,” a new employee was told to stock some shelves. A while later, a manager watches as the employee walks a few feet to a cart, grabs one item, and then walks back to place it on the shelf. The employee doesn’t take it too well when the manager suggests that it might be easier and more efficient to move the cart next to the shelves.
Similar situations often happen in the workplace. Especially if the company does not offer training or does not create policies or procedures to guide new employees.
This is where the Lean manufacturing principle known as standardized work comes in. Let’s discuss what the standardized work principle is, plus how documenting the procedures and ensuring that your employees are sufficiently trained will help your operations run smoothly and efficiently.
What is standardized work?
In Lean manufacturing, standardized work (also called standard work) refers to the process of analyzing and finding the current best practices for performing tasks and processes. These best practices are then documented with detailed steps that define who does the task, what is needed to complete the task, when the task needs to be done, and how to do the task. Sometimes the standardized work instructions might also include details about why the task needs to be performed as documented.
You may ask yourself how this is different from a standard operating procedure (SOP). The answer is in the details. An SOP usually has fewer details than standardized work instructions. For example, a pre-flight SOP might be the safety instructions flight attendants present before takeoff. They don’t all present them in the same way, but they all present the same information.

Standardized work processes are generally more detailed. The step-by-step instructions include details on how to do specific tasks. Describing how things need to be done is important when the process needs to be completed exactly the same way each time to ensure consistent quality and output.
Standardized work and Kaizen methodology
But after you have defined and documented standard work processes and steps, don’t think that you are done. Standardized work includes the documented details of the currently known best practices for doing work. There is always room for improvement. This is why standardized work is considered the foundation of the Kaizen methodology. Kaizen is a Japanese word that means “good change” or “change for the better.” As a business concept, it means to look for ways to continuously improve the way you do your work.
The goals of standardized work and Kaizen are to increase productivity and efficiency and to reduce waste. You can do this by making frequent, small improvements to current processes. After the current best practice is identified, documented, and shared through training, you have a baseline for standard work. Use Kaizen to monitor and evaluate the process. Make small adjustments as needed to create the next current best practice. and make adjustments that will become the next currently known best practice.
Elements of standardized work
Standardized work requires the following three elements:
Takt time
Takt time comes from the German word “taktzeit.” It means clock time or pulse time. In Lean manufacturing, takt time refers to the amount of time you need to create your products so you can keep up with demand. The formula is as follows:
Available production time per day ÷ customer demand per day = takt time
For example, say your employees are scheduled to work an eight hour shift (or 480 minutes). If they have two 15-minute breaks and a 30-minute lunch, the available production time goes from 480 minutes to 420 minutes. If there is a 15-minute briefing before the shift starts and another 15 minutes at the end of the shift for cleanup and general maintenance, the available production time ends up being 390 minutes.
If customer demand is 60 units per day, the takt time says you need to create a unit every 6.5 minutes.
390 minutes ÷ 60 units = 6.5 takt time for each unit
Work sequence
This term refers to the order in which each step in the process must be completed within the takt time.
In-process inventory
This term refers to the amount of materials you need on hand at any given time during the production time. You need to have the right amount for your operators to be able to complete the steps in the work sequence within the specified takt time.
Having too little inventory or too much inventory both lead to waste. When there is not enough material, the work sequence is disrupted, and there is downtime until you come up with additional materials. Too much inventory can lead to overproduction and unsold/unused products.
Benefits of Lean manufacturing standard work
People are often resistant to change. It makes them uncomfortable and forces them to think differently. But standardized work and Kaizen can make change a little easier for everybody because it encourages collaboration and allows everybody to share their ideas for improving the process.
The benefits of using standard work and Kaizen include:
-
Consistent, high-quality output: Because everybody is completing work the same way, there is no variation in the output. When the output is identical, it’s easier to predict costs, required inventory, takt time, work sequences, and so on. Plus, customers will be more satisfied with the consistent quality of your products.
-
Increased efficiency: All workers are completing tasks based on the currently known best practices, meaning that the work flows smoothly and efficiently.
-
Reduced waste: Following specific steps reduces or eliminates defects that can cause products to be discarded or heavily discounted.
-
Safer work environment: Because your employees are well-trained and following standardized work processes, everybody is where they are supposed to be and doing what they are supposed to be doing. This reduces risks and potential injuries.
-
Easier time making improvements: When standard work has been in place for a while, it becomes easier for those involved to see where improvements can be made. Little changes are easier to implement because employees have a better understanding of the process and can quickly see how the change can make the work flow better.
-
Faster problem-solving: Does standard work eliminate problems? No. But when problems come along, it’s easier to fix them because you understand the process and can quickly pinpoint where things went wrong.
-
Focus on processes and not people: When your employees are following standardized work exactly as documented, problems and errors are more likely caused by mechanical or process malfunction. Employees know it is not their fault when something breaks.
Where to start with standardized work processes
Ready to jump in and implement standardized work processes? We’ve put together a few steps to get you started.
Step 1: Analyze current operations
Observe how the work is currently being performed. Gather data such as how many people it takes to produce one unit, how long it takes to produce one unit, which steps are dependent on other steps, and so on.
Perform an as-is process analysis and create a visual process diagram that documents the current workflow. When you understand the current workflow, it’s easier to see where things can be improved.
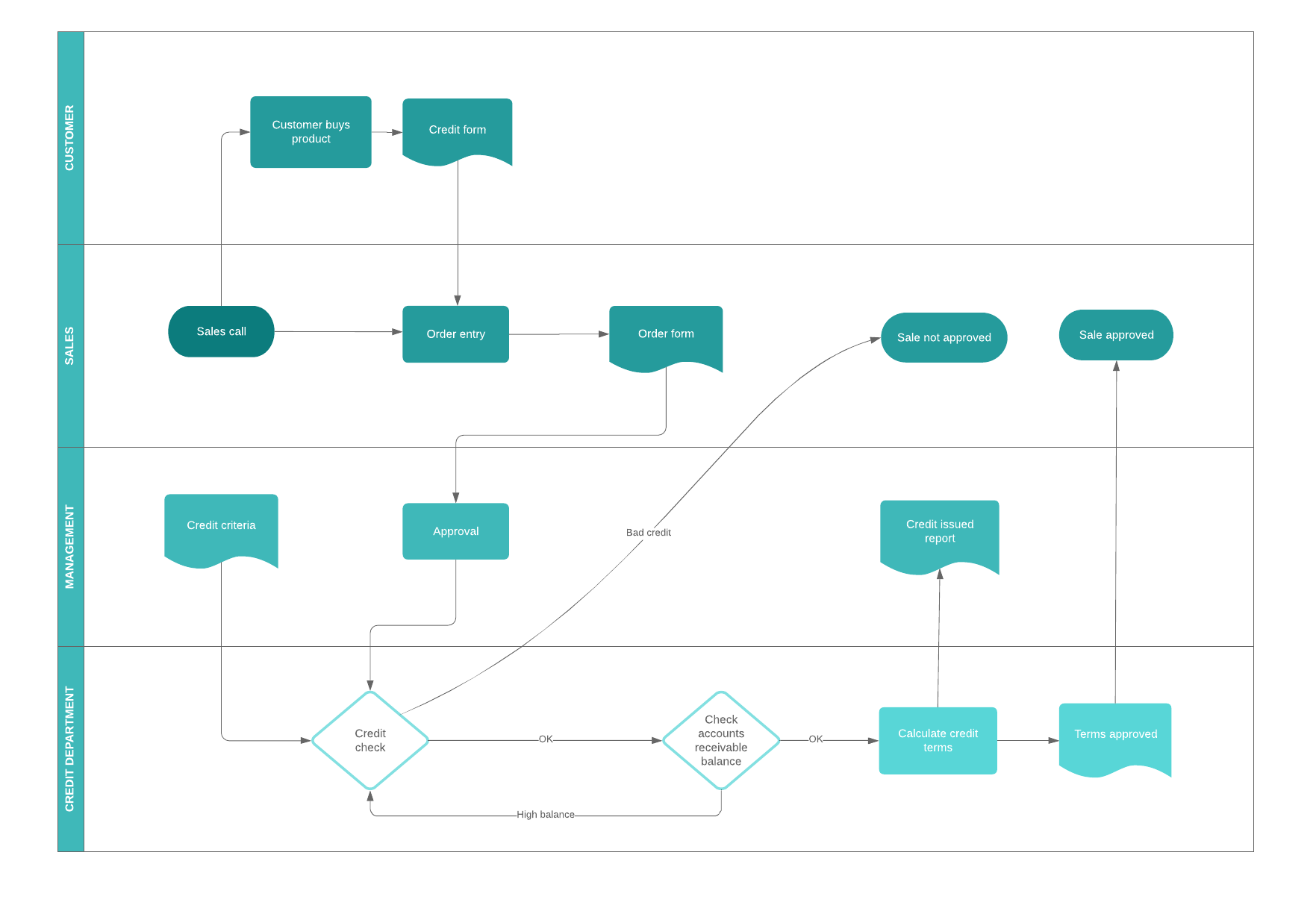
Step 2: Get input when looking for best practices
Many employees have their own way of doing things, which leads to variations in the final output. Many of them may have stumbled across a better and more efficient workflow without even realizing it. Why not let them share their knowledge and experience as you work toward standardization? Give them access to your flowcharts and other visual documents so they can comment and make suggestions.
Collaborating with the operators and listening to their ideas encourages buy-in to proposed changes. It allows them to take ownership of the job and gives them better insight into what needs to be done to get high-quality products out the door.
Step 3: Find the current best practice
As your employees make suggestions and share their knowledge and experience, you should be able to find common practices that they all perform. These common practices can be the basis for defining the current best practice. Look for ways to combine tasks to make the process more efficient.
Create a value stream map to visualize and analyze the steps that employees currently take for each task in the production process. This visual can help you to identify and eliminate the steps that slow down the process or are simply not needed.
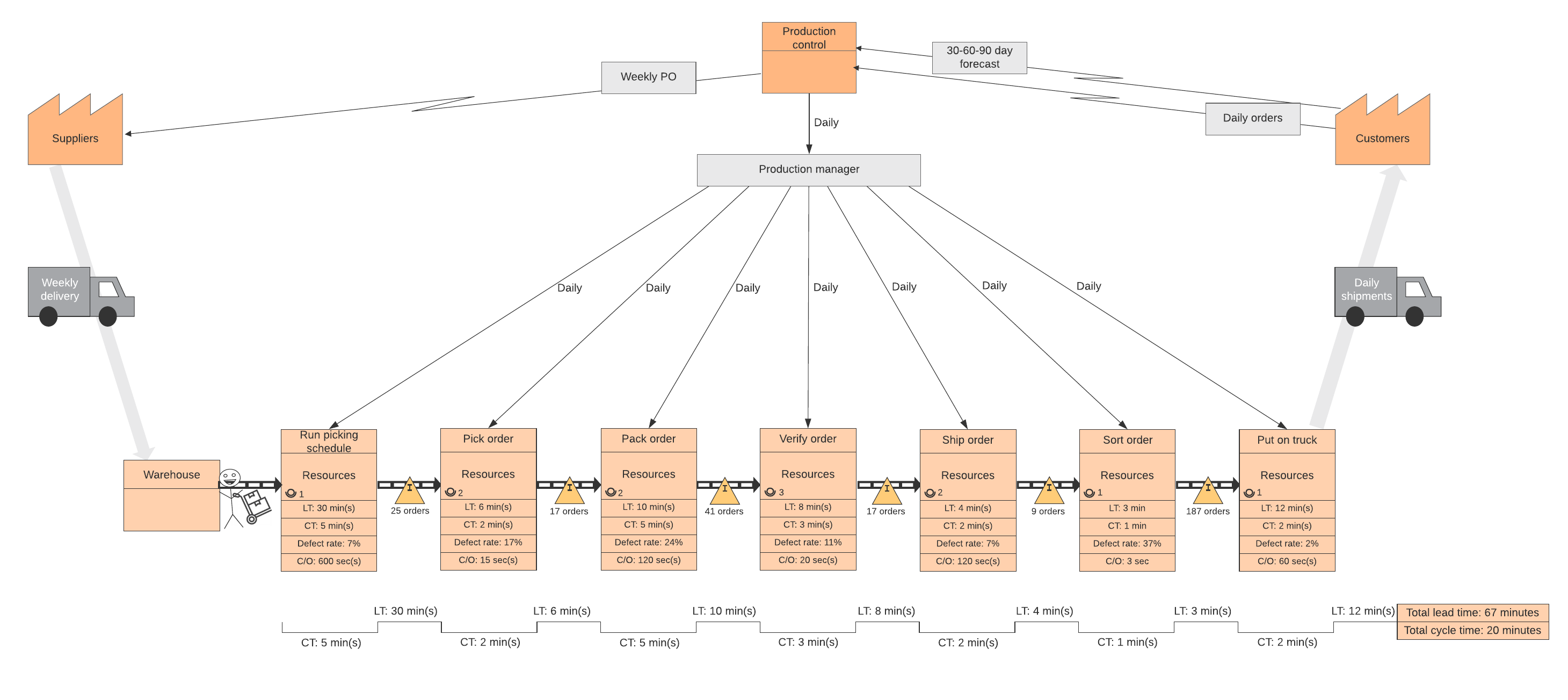
Step 4: Document everything
When you have identified and defined the current best-known practice, document it. The documentation is key to ensuring that everybody follows the exact same procedure.
There are several different ways to document your standardized work—but we suggest that you use visuals to document processes. People learn faster and retain knowledge longer with visual documentation.
Step 5: Provide training
After the processes have been documented, it is important to train everybody on how to follow them. Visual documentation posted at workstations, on walls, or on monitors combined with comprehensive training helps everybody to remember what they need to do.
Step 6: Rinse and repeat
Remember that standardized work refers to the documented currently known best practices. It is not static. You got this far, but the job is not done. It is a living document that allows for updates.
Observe people as they work and follow up frequently to ensure that everybody is adhering to the standardized work process. Ask for input from employees to troubleshoot problems and find more efficient ways to get the job done right. Perform a root-cause analysis to figure out solutions to problems that come up.
Implementing standardized work doesn’t happen overnight. It’s a lot of work to gather data, analyze, figure out the best practices, and document it all. But, once you have done it, the next time is much easier. And the benefits of faster production, higher-quality products, happier employees, and increased customer satisfaction are well worth it.
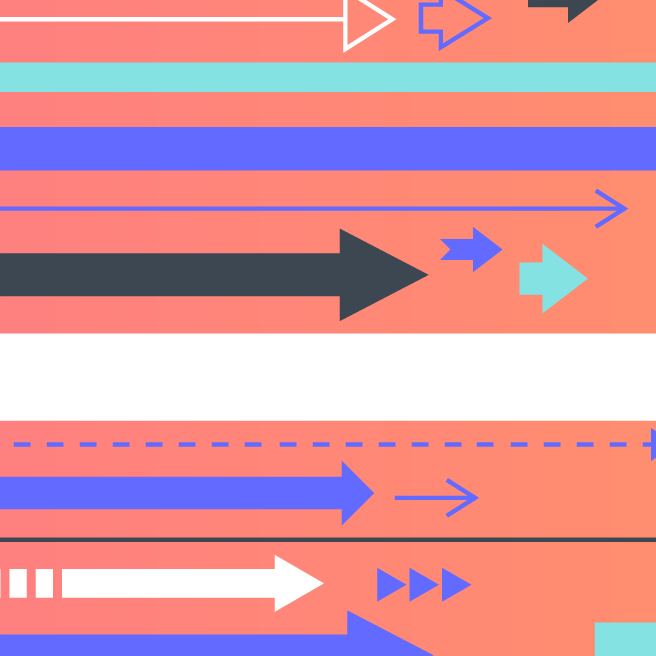
Get started with standardizing workflows using one of these process map templates.
Try one nowAbout Lucidchart
Lucidchart, a cloud-based intelligent diagramming application, is a core component of Lucid Software's Visual Collaboration Suite. This intuitive, cloud-based solution empowers teams to collaborate in real-time to build flowcharts, mockups, UML diagrams, customer journey maps, and more. Lucidchart propels teams forward to build the future faster. Lucid is proud to serve top businesses around the world, including customers such as Google, GE, and NBC Universal, and 99% of the Fortune 500. Lucid partners with industry leaders, including Google, Atlassian, and Microsoft. Since its founding, Lucid has received numerous awards for its products, business, and workplace culture. For more information, visit lucidchart.com.
Related articles
Why you need the Lean PDCA cycle to improve your iterative process
Learn about the PDCA cycle and how it improves iterative processes, reduces waste, and creates better products.
How to apply the Plan-Do-Check-Act (PDCA) model to improve your business
The Plan-Do-Check-Act cycle helps teams transition to a culture of continuous improvement. Learn how the cycle works and how to implement it.