Let’s say your company leads the market within your industry. You could easily just keep doing what you’ve been doing. Evidently, it’s worked well for you—if it’s not broken, don’t fix it, right? This approach can work for a while, but you risk becoming complacent.
History is full of companies that became complacent after reaching success. And complacency eventually led to a lack of innovation, failure to embrace new technology, and the inability to adapt to changing market trends. When a company becomes stagnant, it risks losing everything as customers look for other ways to meet their needs.
Successful companies understand that change and improvement are essential for business growth and market share. In this article, we’ll discuss how the Lean methodology can help you to improve productivity, eliminate waste, and keep your customers happy.
What is Lean methodology?
The Lean methodology, also known as Lean manufacturing, Lean thinking, or Lean management, is used to maximize value and quality while minimizing waste.
Lean focuses on customer centricity, meaning the customer is at the center of everything you do. Customer needs and wants drive decision-making, development, processes, and operations to ensure a positive customer experience.
Lean’s roots can be traced to Japan in the 1940s and 1950s, as the country focused on rebuilding industries and improving the economy after World War II. One of the first philosophies to emerge from the collective effort was Kaizen, which means “change for the better” or “continuous improvement.” The Toyota Motor Corporation used the ideas in Kaizen to develop the Toyota Production System (TPS), which emphasizes efficiency, quality, waste reduction, and continuous improvement.
The success of TPS captured global attention from companies wanting to learn how they could continually improve, boost efficiency, and produce high-quality goods while eliminating waste.
TPS formed the foundation of Lean methodology. Researchers James P. Womack and Daniel T. Jones introduced Lean in the early 1990s in their book The Machine That Changed the World, which helped popularize Lean principles outside of Japan.
While the Lean methodology was originally developed for optimizing efficiencies in manufacturing, it has been applied to other industries such as healthcare, software development, hospitality, construction, and beyond.
Pillars of Lean
Lean methodology includes several principles, also called the pillars of Lean, that organizations use to guide the implementation of Lean practices.
Value
Because Lean principles focus on the customer, you must define what is valuable to your customers. This means identifying the features, attributes, and outcomes the customers are willing to pay for. Don’t include “cool to have” features or functionality if your customers don’t need or want them. By identifying what is of value to the customer, you eliminate the waste of time and resources on things that don’t matter.
Use our free value proposition template to ensure that the products you develop or manufacture will meet your customers' needs.
Value stream mapping
A value stream is the sequence of processes, steps, and activities involved in developing and delivering products and services of value to your customers.
A value stream map lets you visualize the value stream. This involves identifying and categorizing the flow of all the information, materials, and processes that turn your inputs into products or services.
This free value stream map template can help you visualize and analyze the events that must happen throughout a project until the product is delivered to the customer.
Workflow
The aim of this pillar is to create a smooth workflow that won’t be interrupted by bottlenecks or disruptions. Creating a process workflow chart can help you identify areas that could cause problems and impede your workflow. Identifying problem areas early on makes finding solutions easier so the work continues as expected.
A workflow chart can also help you analyze how well current processes work so you can continuously look for ways to improve them.
Pull systems
In a pull system, work is aligned with customer demand. Work is completed based on actual demand instead of anticipated demand. This minimizes waste by ensuring that resources are only used when needed, limiting overproduction.
Continuous improvement
This pillar emphasizes creating a culture of continuous improvement. Employees at all levels are encouraged to analyze current processes, identify improvement areas, and implement small incremental changes to increase efficiency. This will help you to improve quality and deliver increased value to your customers while you reduce waste, inconsistencies, and possible defects.
Respect for people
Companies need to value and respect their employees. Involving your employees in the company’s improvement efforts empowers them to share knowledge and skill. When employees feel their contributions are important, it gives them a sense of ownership in developing your products and services. That sense of ownership encourages collaboration and teamwork, builds trust, and establishes a supportive work environment, which can also help in employee retention efforts.
Visual management
Use visual collaboration tools like Lucidchart to make your projects more visible and transparent. Displaying charts, schedules, boards, and diagrams in a prominent space gives employees an overview of the project’s current state. Understanding what work has been done, what is being done, and what still needs to be done keeps everyone on the same page.
A visual representation of your processes and workflows also makes it easier to find potential problem areas so you can fix them before they cause delays.
Standardization
Developing and implementing standard processes helps you establish best practices, so your work and delivery methods are consistent. Once you identify deviations and roadblocks, you can quickly develop and implement improvements with little to no downtime.
Lean in software development
The concepts in the Lean methodology originally applied to manufacturing, but software development was one of the next industries to adopt it.
In the context of software development, Lean is the same as it is in manufacturing. The focus is on efficiently and effectively adding value to software applications that meet customer needs.
Lean lets software development teams improve efficiency, reduce costs, eliminate waste, standardize processes, increase productivity, and maximize customer satisfaction. When combined with Agile methodologies like Scrum, Lean lets teams quickly respond and adapt to changing customer requirements by adding value incrementally in short iterative cycles.
Lean tools
There are several tools you can use to help you implement Lean practices in your workplace. These tools are designed to help you:
- Focus on customer-centric product development
- Identify and eliminate waste
- Boost efficiency
- Increase the overall value of your products
We have hundreds of templates to get you started. Here are a few to consider.
Affinity diagram
An affinity diagram helps you gather and sort data to consolidate similar ideas and information. From there, you can analyze the data and prioritize the best ideas and solutions to address customer concerns and meet their expectations.
Kanban board
The Japanese word “kanban” means sign or billboard. A Kanban board is a visual management tool that divides your work into three columns: items you need to do, items you’re working on, and completed items.
As new tasks or work items are added to a project, they are written on a card and placed in the “To do” column. When a team member chooses an item to work on, its card is moved to the “Working on” column. The card is moved to the “Finished” column after completing the work item.
Kanban boards help you manage your workload balance, track progress, and identify potential bottlenecks or disruptions.
5S dashboard
This tool is used to help you organize your workspace to maximize efficiency. The 5S dashboard includes the following sections:
- Sort: Identify unnecessary items in your workspace and remove them.
- Set in order: Arrange the necessary items where they are most easily accessible for their function.
- Shine: Clean your workspace and tools regularly.
- Standardize: Establish consistent and repeatable processes and procedures to maintain the first three practices.
- Sustain: Create a culture where employees consistently follow and adhere to the 5S principles.
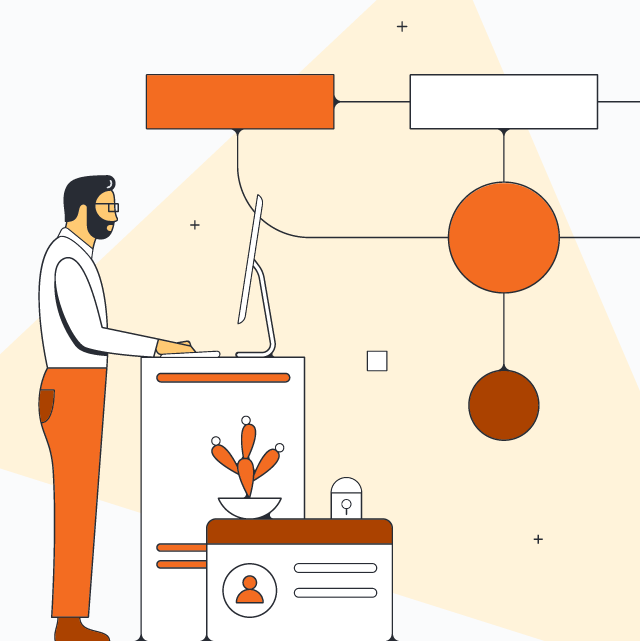
Explore hundreds of Lucidchart templates to level up your productivity.
Go nowAbout Lucidchart
Lucidchart, a cloud-based intelligent diagramming application, is a core component of Lucid Software's Visual Collaboration Suite. This intuitive, cloud-based solution empowers teams to collaborate in real-time to build flowcharts, mockups, UML diagrams, customer journey maps, and more. Lucidchart propels teams forward to build the future faster. Lucid is proud to serve top businesses around the world, including customers such as Google, GE, and NBC Universal, and 99% of the Fortune 500. Lucid partners with industry leaders, including Google, Atlassian, and Microsoft. Since its founding, Lucid has received numerous awards for its products, business, and workplace culture. For more information, visit lucidchart.com.
Related articles
7 essential steps to create a process improvement plan [+templates]
No matter how good the idea, changes won't last without a solid process improvement plan in place. Learn the essential steps involved with every process improvement plan.
What is a workflow? Benefits and examples of repeatable processes
Ensure that important processes are completed the right way, every time. In this article, we will explain why your business needs efficient workflows and show you some workflow examples to help you get started.