5 Lean Six Sigma principles you should adopt immediately
Lucid Content
Reading time: about 10 min
Topics:
5 Lean Six Sigma principles to boost efficiency
Every project manager shares the same basic goal: they want to streamline workflow and eliminate unnecessary or repetitive tasks in order to plan and execute projects as efficiently as possible. However, project managers can choose from several methodologies to get there.
If you’ve read our other content about process improvement methodologies, you’ve probably noticed that two schools of thought dominate project management philosophy: the Lean method and the Six Sigma approach. The Lean method stresses the importance of reducing all forms of waste. Six Sigma is a data-driven, tried-and-true project management process.
Combine these two philosophies, and you get the Lean Six Sigma methodology. Learn the basic principles of Lean Six Sigma below and discover whether it's right for your team.
Lean vs. Six Sigma
Although they combine to become complementary, Six Sigma is different from Lean in its origin, focus, and methods for improving processes.
Six Sigma has been the quintessential project management method with its belt-based certifications since 1986. Typically, the principles of Six Sigma uses a five-step approach to solving issues, either the DMADV or DMAIC methodology. Ultimately, the goal is to reduce product variations and defects using statistical analyses. As happy as businesses have been with Six Sigma, Six Sigma has some shortcomings that cause many to wonder how they can improve the process.
Lean is a philosophy centered around eliminating waste and providing the best customer experience. According to the principles of Lean methodology, there are eight kinds of waste: defects, overproduction, waiting, non-utilized talent, transportation, inventory, motion, and extra processing. By using a value stream map to document the steps involved in producing a product or delivering a service, Lean sets out to find and eliminate that waste.
So what happens when you turn up the heat and combine best practices?
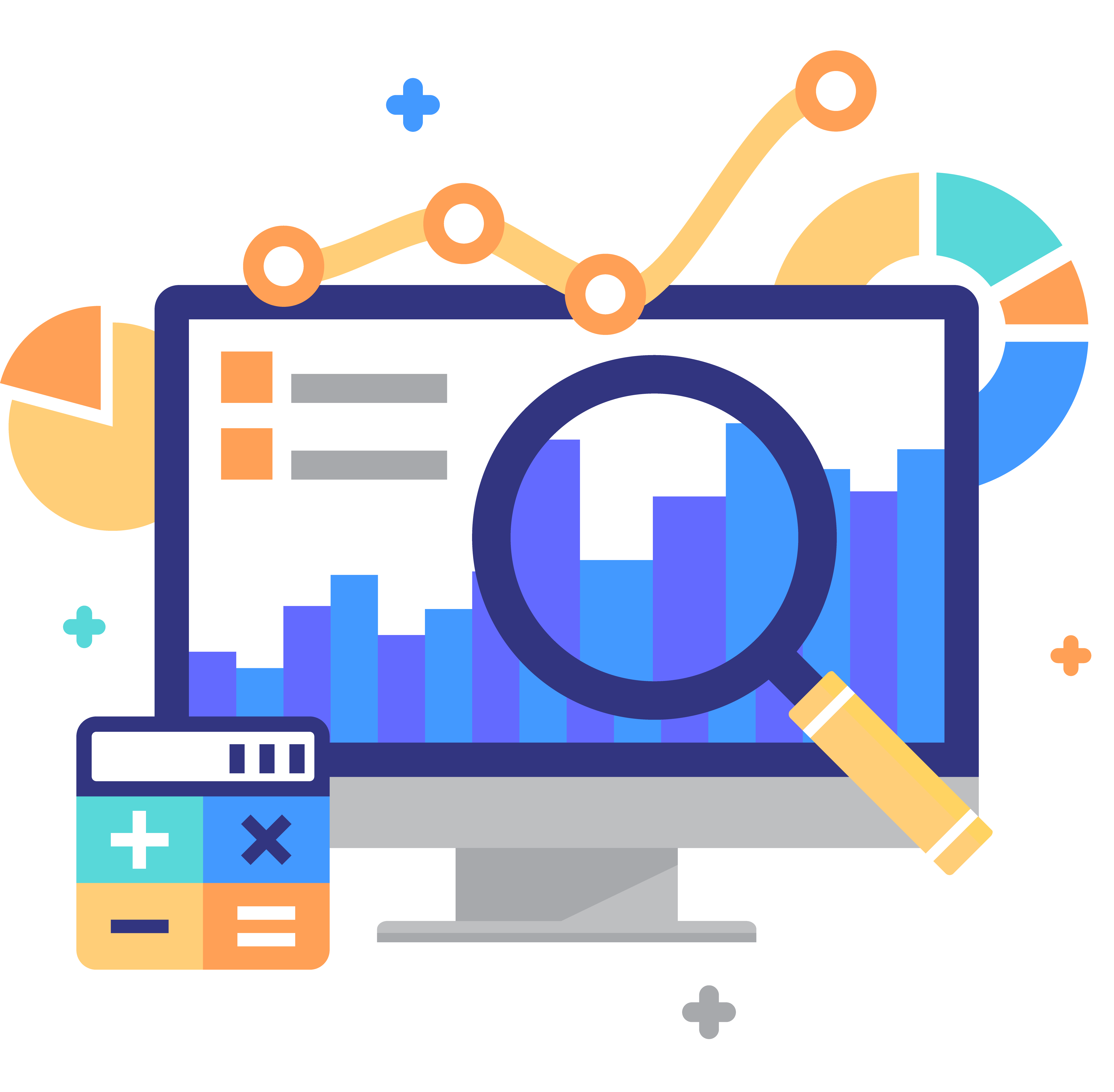
Want more details on the differences between Six Sigma and Lean?
Read moreWhat is Lean Six Sigma?
Because it marries these two process improvement methodologies, Lean Six Sigma gets the best of both worlds. It not only reduces process defects and waste, but it also provides a framework for overall organizational culture change. By introducing Lean Six Sigma principles, the mindset of employees and managers change to one that focuses on growth and continuous improvement through process optimization. This change in culture and the mindset of an organization maximizes efficiency and increases profitability.
Lean Six Sigma principles
For a process stream that produces the best results, consider the following Lean Six Sigma principles for your organization.
1. Focus on the customer
One of the oldest, yet most prudent, pieces of business advice holds true today. No matter what business you’re in, you should always put customers first. Everything should revolve around your customers and their needs. After all, without customers, where would your organization be?
Before you start making any drastic or even minor changes, establish the level of quality or requirements that you have promised your customers. Every decision you make should bring your company closer to delivering maximum value.
2. Map out the value stream
Before you can improve your process, you have to know all the steps in it. Even if you already document your workflows, it’s important to examine how you do things to determine which steps add value and which do not (and can, therefore, be removed from the process).
Understand how the current process works
You need to see the current state of your process before you can move forward and make improvements. Identifying your value stream is indisputably what makes Lean Six Sigma principles so effective. It's how businesses visualize all of the steps in a given process and highlight areas of waste.
One way to do is to build a value stream map, which is a flowchart that illustrates and analyzes the steps in a production or service process. For example, if you were trying to figure out your value stream for building a car, your value stream map would include purchasing parts, assembling them (and checking for quality assurance), and distributing the finished product.
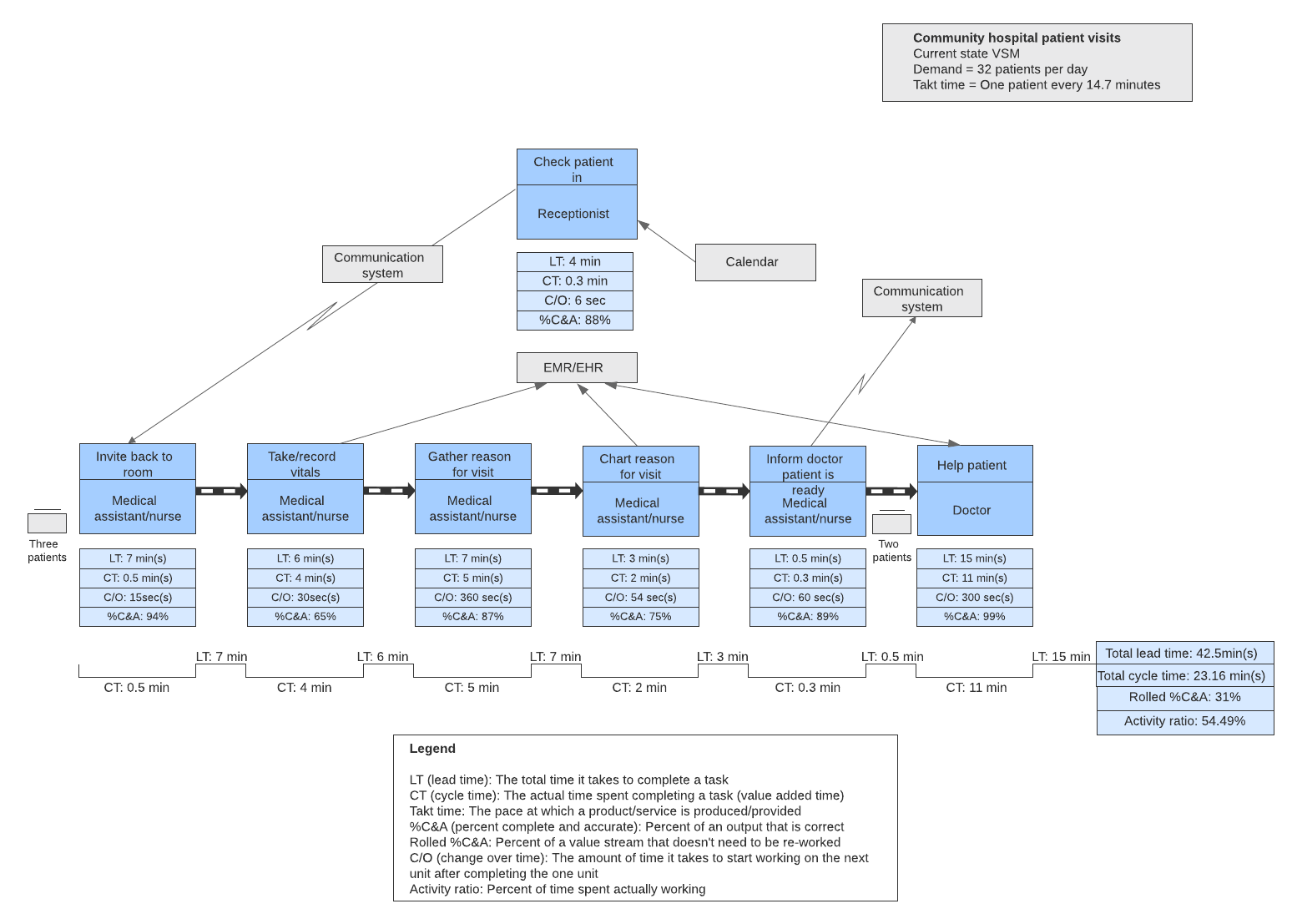
Get the big picture view of your process from start to finish. That way, you don't risk focusing too much on a single area and optimizing it at the cost of another step in process.
Identify the root cause of problems and bottlenecks
Once you have put together your current value stream, you can identify the problems in your workflow and investigate their root cause.
To find out what’s currently causing problems, perform a root cause analysis with a cause-and-effect diagram. Also known as fishbone diagrams due to their shape, they identify problems within different areas of your business. For example, service industries typically look at the four Ps—policies, procedures, people, and the plant/technology—to find potential causes.
Another way to tease out the cause for a problem is the 5 Whys analysis. Suited to somewhat difficult but not overly complex problems, the 5 Whys analysis takes a problem and ask “Why?” five times, each time trying to dig deeper into the answer until the original cause comes to light. If multiple causes arise, then the problem might be too complicated for this approach and would likely benefit from a cause-and-effect analysis instead.
3. Remove waste to create flow
Before you can make improvements and create flow in your process, you need to visualize and remove waste. That sounds like a simple step, but both Lean and Six Sigma teach that inefficiencies can sometimes be hidden, which is why it’s so important to first know what counts as waste and then understand how to reduce variations.
Remove waste and non-value added steps
Combining the two methodologies, waste in Lean Six Sigma is both anything that doesn’t add value to the final product and anything that doesn’t meet the customer’s expectations. That leaves a lot of room for things to go wrong and areas that need improvement to get overlooked.
To be more proactive about removing waste, try these five steps from Rene T. Domingo, professor at the Asian Institute of Management.
Step 1: Make waste visible.
If you don’t see waste, then you can’t eliminate it. Remember, there are many different kinds of waste according to Lean manufacturing, including defects, overproduction, waiting, non-utilized talent, transportation, inventory, motion, and extra processing.
Step 2: Be conscious of the waste.
Acknowledge waste as waste. For example, we might take it as a matter of course that we’ll be kept waiting at a doctor’s office or a hospital. But that is waste that could be eliminated by having a better scheduling system, sorting patients more efficiently at check-in, or hiring more personnel.
Step 3: Be accountable for waste.
Embrace the principles of Lean Six Sigma, and encourage a culture of responsibility and ownership in your organization. No one wants to be a source of inefficiency, but if everyone on the team focuses on reducing waste, then you’ll foster a culture of accountability where everyone is working for the same goal.
Step 4: Measure the waste.
This step is important for getting buy-in from both team members and executives. Change, especially in larger organizations, can seem more costly than keeping the status quo, and employees also won’t be motivated if the waste seems trivial. It’s hard to eliminate waste if you don’t know the full extent of it.
Step 5: Eliminate or reduce the waste.
While it may be tempting to stop at this stage, this should be an ongoing process of review and revision. Adding new employees, changing or making new products, offering new services, changing locations, etc.––there are always more opportunities to cut waste and optimize your business.
Reduce variation and increase standardization
Borrowed from the principles of Six Sigma, reducing variation and increasing standardization makes it possible for organizations to be more cost efficient and have higher customer satisfaction.
Getting things right every time––or almost every time––can be challenging, so here are a few ways to get started:
-
Document your processes: As mentioned previously, you won’t know how to improve, optimize, and standardize without a clear view of how things are currently done.
-
Establish and share best practices: Reducing information silos also benefits your processes; encourage the sharing of good ideas throughout the organization.
-
Create checklists for processes so everyone knows and follows the same steps: This will make it much easier for new employees to get up to speed while also reducing errors that existing employees are likely to make.
-
Make sure everyone gets the same training: Getting your processes working just right means that all your employees need to be on the same page.
-
Use forms and templates: This greatly reduces confusion for employees when creating reports, responding to customers, logging errors, etc.
-
Automate anything that’s repetitive, boring, and therefore error-prone: Speed things up and make them more precise by replacing some manual tasks, especially if there’s an online application or tool that can do it better.
4. Communicate with your team
People don’t like change, which means that in your organization, your employees will likely keep doing what they’re doing unless management tells them otherwise. The onus is on the business to effectively, clearly communicate new standards and practices. Be sure each employee receives training and feedback on the new processes and procedures. Otherwise, why expect the problem to change?
Ways to communicate and disseminate information include:
- Creating new knowledge by putting a knowledge base in place or updating your existing knowledge management system
- Updating your customer support knowledge base
- Making the full process easily accessible for stakeholders and employees according to their specific role
- Creating process maps that show your employees what has changed about their workflow
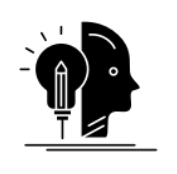
Learn more about process maps and how they can help you implement Six Sigma principles.
Read now5. Create a culture of change and flexibility
As you can tell from the other principles we’ve discussed, Lean Six Sigma requires a lot of change. You need to welcome change and encourage your employees to accept change as well. The root of this cultural change should be data. You can dispel fears by explaining the benefits of the change and showing employees how you have made their work more impactful through data.
Six Sigma brings in a highly scientific and rigorous approach to examining, quantifying, and analyzing data, which is essentially the DMAIC process that we mentioned earlier. But the point isn’t to just do that once and then discard it until a new problem arises. It should become an integral and intrinsic part of your everyday, every project mindset.
As part of this cultural shift, your company should always look for new ways to streamline the process and remove waste. Keep your eye on the data, examine your bottom line, and adjust your processes where necessary.
Lean Six Sigma methodology captures the best of both Six Sigma and Lean methods of project management. If you decide to follow this methodology, follow the Lean Six Sigma principles and optimize process improvement once and for all.
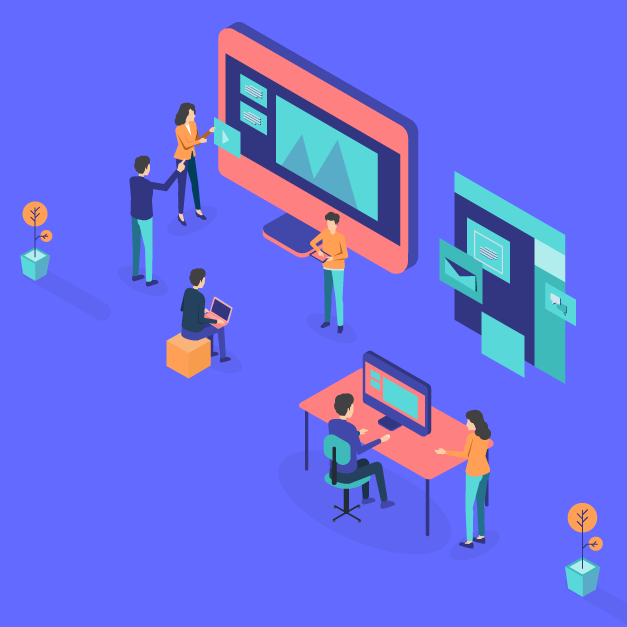
Check out the best Lean Six Sigma tools for process improvement.
Read nowAbout Lucidchart
Lucidchart, a cloud-based intelligent diagramming application, is a core component of Lucid Software's Visual Collaboration Suite. This intuitive, cloud-based solution empowers teams to collaborate in real-time to build flowcharts, mockups, UML diagrams, customer journey maps, and more. Lucidchart propels teams forward to build the future faster. Lucid is proud to serve top businesses around the world, including customers such as Google, GE, and NBC Universal, and 99% of the Fortune 500. Lucid partners with industry leaders, including Google, Atlassian, and Microsoft. Since its founding, Lucid has received numerous awards for its products, business, and workplace culture. For more information, visit lucidchart.com.
Related articles
Six Sigma process mapping: Why it matters and how to get started
Learn everything you need to know about Six Sigma process mapping, including benefits, step-by-step instructions, and different types of process maps you can use.
Which process improvement methodology should you use?
Struggling to decide which process improvement methodology to use? Learn about the top approaches—Six Sigma, Lean, TQM, Just-in-time, and others—and the diagrams that can help you implement these techniques starting today.