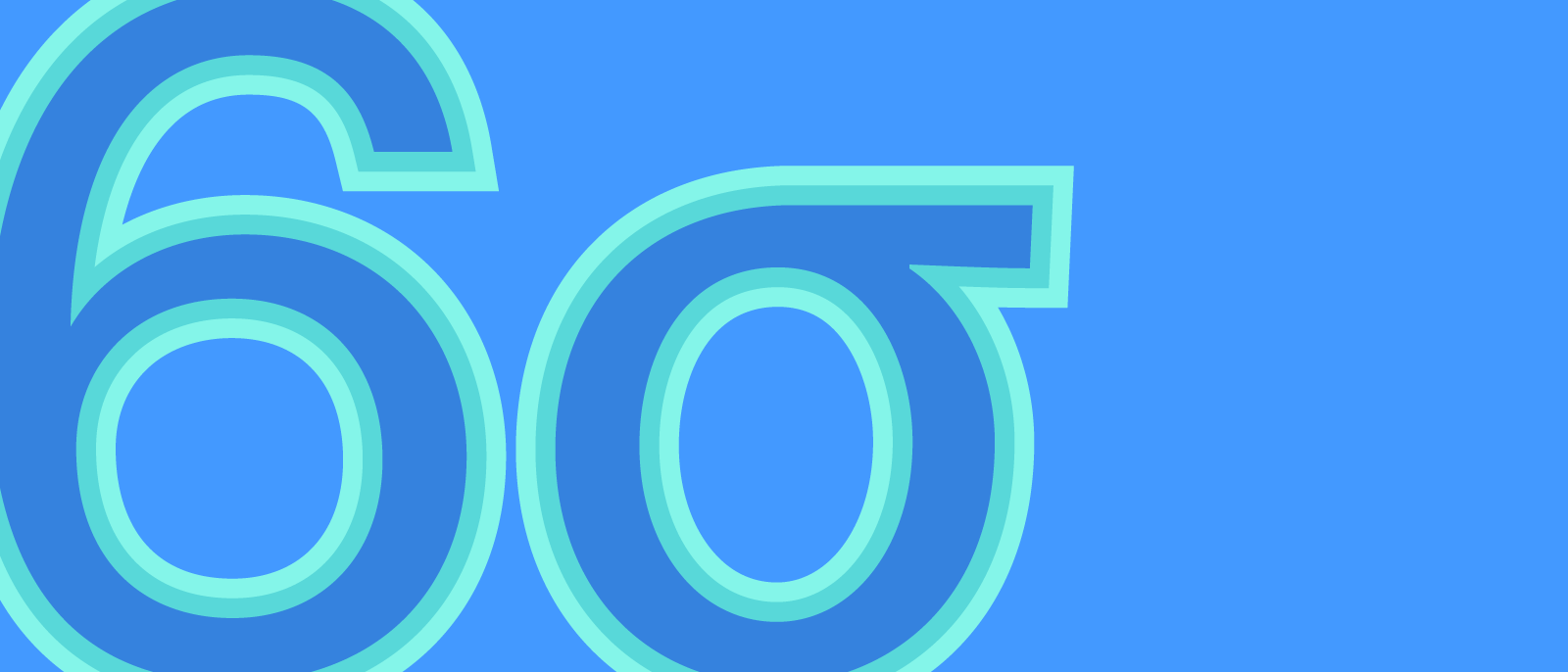
Limitations of Six Sigma Steps and What to Do About Them
Lucid Content
Reading time: about 6 min
What is the goal of any project management methodology? To eliminate waste and streamline processes.
With that in mind, it’s easy to see why Six Sigma became so popular and why so many industries have scrambled to find ways to apply it. Who doesn’t like to accomplish tasks faster while saving money?
However, if it's incorrectly applied, Six Sigma can do more harm than good. In the quest to refine processes and eliminate waste, Six Sigma may limit flexibility for unique circumstances, and leave less room for innovative new tools or methods.
Let’s review what makes up the process of Six Sigma, how to follow the Six Sigma steps, where the limitations of the methodology lie, and what methods or tools companies may want to use instead.
To get started, here's an overview of the Six Sigma steps that you can easily customize and share with your team.
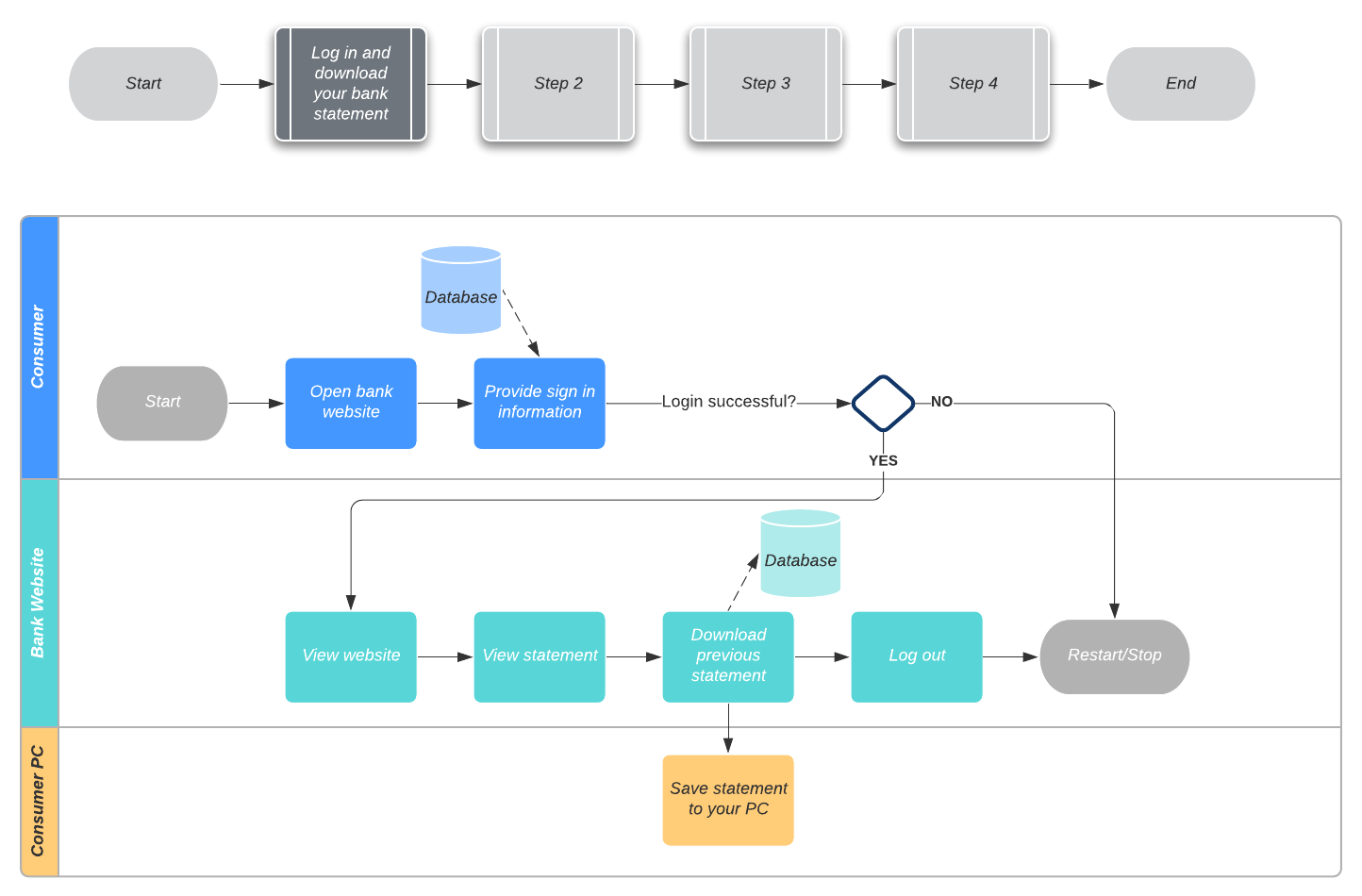
What is Six Sigma?
The Six Sigma methodology was developed in the mid-1980s by engineers at Motorola as a way to improve manufacturing processes. At its core, Six Sigma involves collecting and leveraging data to eliminate defects and waste in manufacturing, with the end goal of improving overall efficiency and quality.
The term “sigma” is a measurement of how far from perfect a system or producer can get—by Six Sigma standards, companies should reduce manufacturing defects to less than 3.4 per 1 million units.
Businesses use the Six Sigma methodology to improve processes by identifying the errors that lead to defects and implementing new management systems once errors have been addressed. The methodology is most effective with repetitive, assembly line-style operations where individual steps can be isolated, examined, and improved upon.
How is Six Sigma used?
Originally developed for manufacturing, Six Sigma can now be found across many industries. However, just because companies in different sectors have applied this methodology doesn’t necessarily mean that these companies have used it correctly or effectively. Outside of a manufacturing operation, Six Sigma often fails to yield the kind of results needed to justify such a time-consuming and expensive management change.
To function effectively, Six Sigma requires buy-in from everyone involved. It requires a sizable upfront cost to implement and train employees on the methodology of Six Sigma and its execution.
Employees of all levels must be trained in the various positions of the methodology as well. Individuals who have completed a Six Sigma certification class earn belts to designate their level—Green Belts are for beginners, Black Belts are for project leaders, and Master Black Belts are for those in charge of implementing Six Sigma throughout the business.
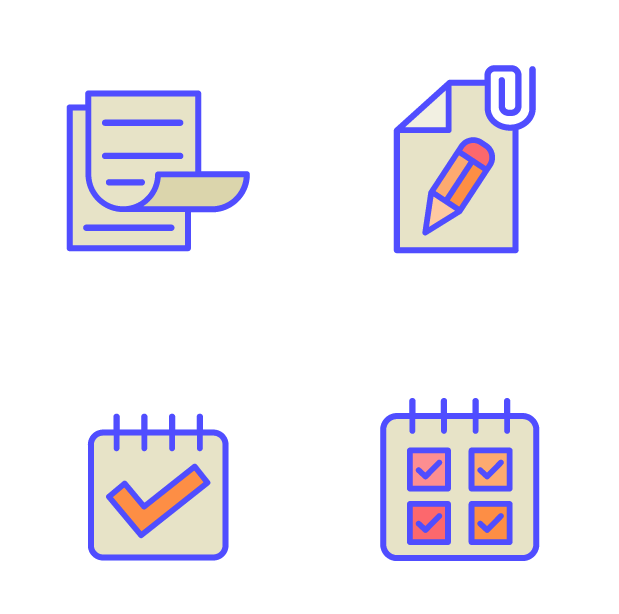
Get started improving your own processes when you implement Six Sigma process mapping.
Learn moreWhat are 5 steps for Six Sigma?
The Six Sigma steps for process improvement, also referred to as DMAIC, are fairly direct and straightforward.
- Define the problem. Craft a problem statement, goal statement, project charter, customer requirement, and process map.
- Measure the current process. Collect data on current performance and issues. Verify that the data is reliable, and update the project charter as needed.
- Analyze the cause of issues. Examine the process and data that was collected, display the data, investigate and confirm what’s causing the issues, and continue updating the project charter as needed.
- Improve the process. Decide on solutions to fix issues and create process maps for those new solutions. Take steps to implement the new fixes and continue to measure improvement.
- Control. Refine the new process, continue monitoring, and use findings elsewhere in the business, if possible.
What are the limitations of Six Sigma?
One of the challenges of the fact-driven process of identifying a problem and working toward a solution is that it tends to leave out a key component: humans—and more importantly, how humans impact and work through different obstacles. Sometimes it is often beneficial to give employees a chance to tackle issues head-on before investing in a complete operational overhaul.
The one-size-fits-all approach to Six Sigma can also be somewhat limiting at times, especially within organizations or disciplines that rely on creativity. Employees who crave the freedom to toss caution (and sometimes process) to the wind in an effort to innovate may find the Six Sigma process stifling.
Six Sigma also does not technically allow for the introduction of new tools or methods, even when they could be beneficial. Since Six Sigma generally requires total dedication across all teams, it’s difficult to use or experiment with other process methodologies for other areas of the organization.
What can you use instead of Six Sigma?
Dozens of project management methodologies exist with varying degrees of structure, rules, and processes. Here are just a few of the most common:
Waterfall methodology: Made up of discrete, sequential tasks, the waterfall methodology for project management ensures each step is completed in the correct order to achieve the final product.
Scrum methodology: As an agile methodology, scrum uses an incremental approach that allows for small teams to work simultaneously on deliverables, testing and adjusting course throughout to complete projects quickly.
Kanban: Relying on notecards to visually represent and prioritize project tasks, Kanban boards track the project through stages to keep everyone on the same page.
Agile methodology: Driven by customer needs, Agile produces deliverables using iterative cycles to continuously refine until a final product is created.
To decide which style is ideal for your project or organization, try working backward. Start with what you want your end product to look like.
Borrow from Six Sigma principles and conduct a fact-finding mission, evaluating where your team is already successful, what’s working well, and what type of environment drives those ideal results. Does your organization do best in large teams or small teams? Do team members like two-week sprint schedules or more free-form processes? Use the information you’ve gathered as a guide to investigate which project management methodology works for your specific goals, constraints, and timelines.
Keep track of the pros and cons of each type of project management style, and decide with key stakeholders which process makes the most sense for your unique situation.Determine the best methodology to meet your needs with the ultimate guide to project management methodologies and make sure your project goes off without a hitch.
You don’t need to stick rigidly to the rules of just one project management process. Rather, be open to taking the best parts of different methods and using them to your advantage.
Beyond Six Sigma
Six Sigma should be recognized and celebrated for what it is: a data-driven approach to streamlining production and manufacturing. For industries and businesses outside of manufacturing, though, teams should explore more flexible project management or process improvement methodologies. For all its successes, Six Sigma can’t replace human ingenuity and hard work. Look instead to the brain power in your organization, and find a methodology that works with your team’s creativity and can be customized where needed.
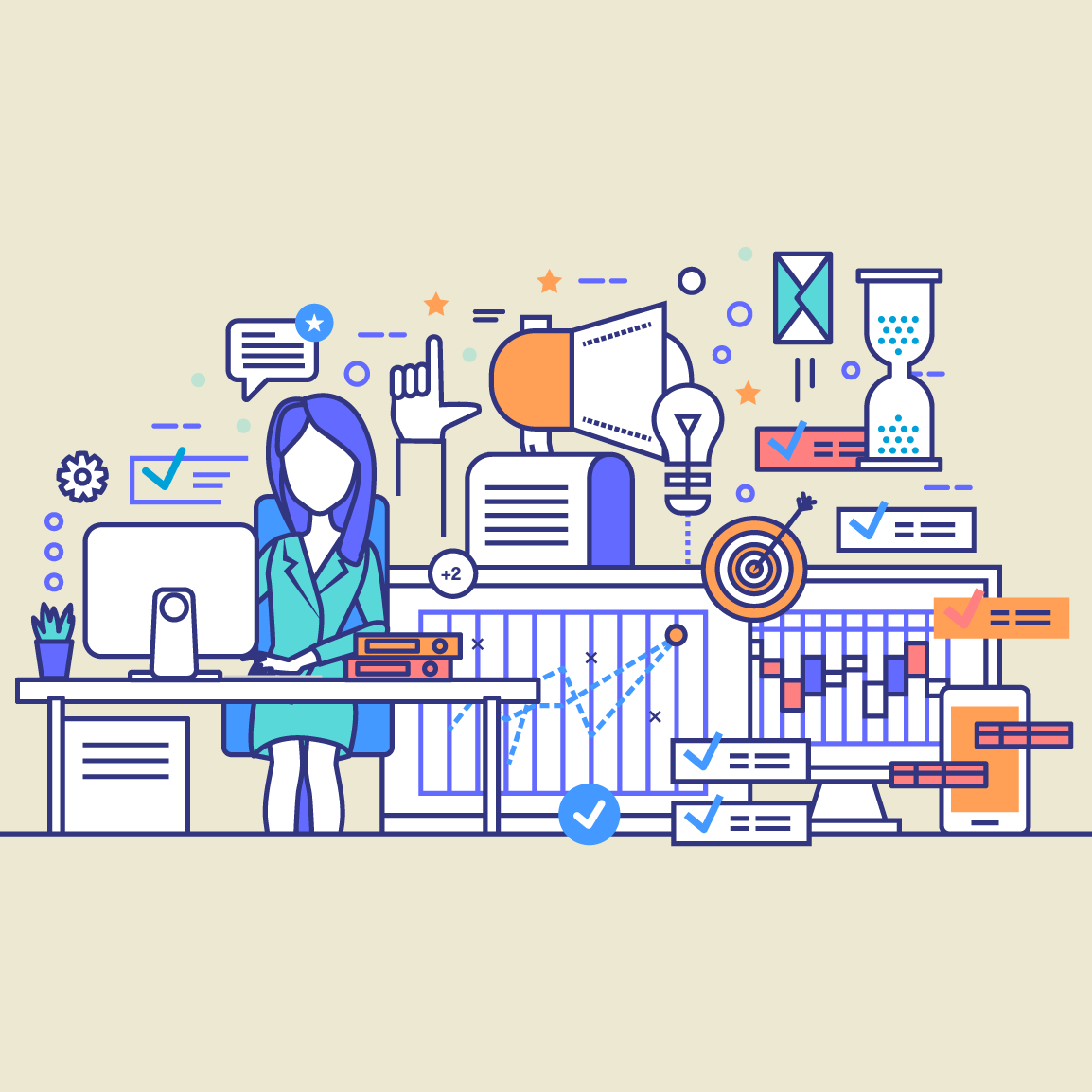
New to project management? Check out this guide for beginners to get your started on the right foot..
About Lucidchart
Lucidchart, a cloud-based intelligent diagramming application, is a core component of Lucid Software's Visual Collaboration Suite. This intuitive, cloud-based solution empowers teams to collaborate in real-time to build flowcharts, mockups, UML diagrams, customer journey maps, and more. Lucidchart propels teams forward to build the future faster. Lucid is proud to serve top businesses around the world, including customers such as Google, GE, and NBC Universal, and 99% of the Fortune 500. Lucid partners with industry leaders, including Google, Atlassian, and Microsoft. Since its founding, Lucid has received numerous awards for its products, business, and workplace culture. For more information, visit lucidchart.com.